Operational Excellence Project with NewFlyer Industries
I successfully finished an OpEx course that provided a solid understanding of Operational Excellence through the application of its principles to address real industry problems. The course was heavily focused on practicing lean manufacturing and Six Sigma discipline, and emphasized on identifying and solving problems.
The project was with NewFlyer Industries and the problem we needed to tackle was the cracking of the 60-foot articulated bus join panels. We used the Quality Journal steps which are as follows:
- Define the problem. This is done through creating a charter and understanding the process
- Establish the focus. This is done through the problem statement, the objective, and the progress measure and metrics
- Examine the current situation
- Analyze the root cause
- Act on the cause
- Study the results
- Standardize the change
I created a DOE (Design of Experiments) to test the identified variables that could cause cracking on the panels and understand their effect. After identifying the root cause, I wrote a report and presented our findings to the Director of Operations at NewFlyer. I also implemented 5 quick Kaizens for the issues that were identified as quick hits on the effort vs. value matrix.
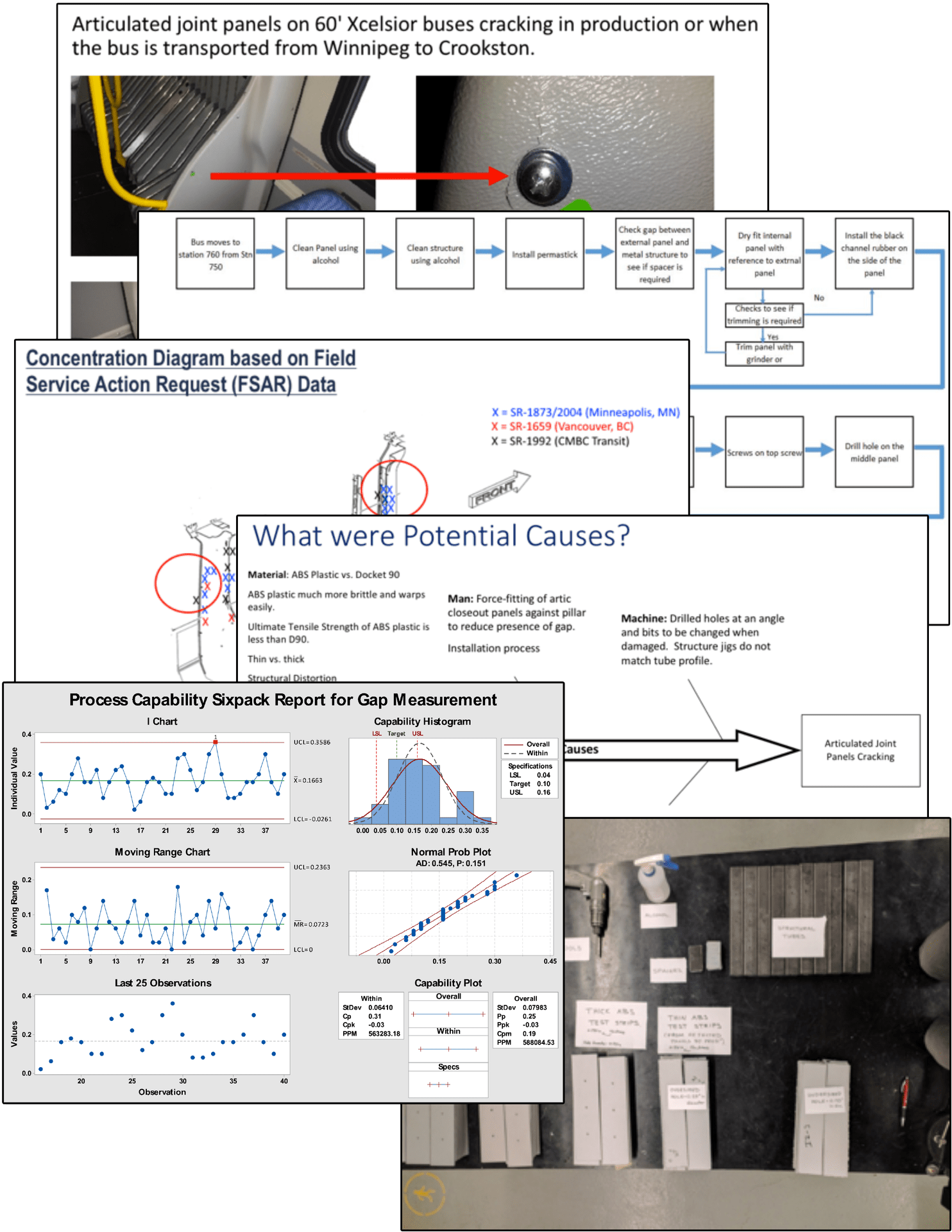
Ham Line Tumbler/Skinner Station
I improved the production efficiency of the ham line tumbler/skinner station by conducting thorough analysis and implementing significant modifications:
- Conducted a statistical analysis to determine that ham delivery to the tumbler was the main source of variation.
- Adjusted the angle of the ham tumbler in accordance with the equipment drawings, improving its purging capability.
- Identified the skinner station as the bottleneck through time study analysis.
- Determined the root cause of the bottleneck at the skinner station using a "5 Why's" analysis. The extended handling times introduced operator fatigue.
- Concluded that two skinner stations were insufficient for our new cut floor speed by comparing cycle times with the old production floor.
- Used AutoCad Inventor to redesign the skinner stations for improved product flow.
- Assisted in the redesign of the ham line by sharing my findings with the equipment supplier's design engineer.
Rework Area Kaizen Event
I was part of a team that included process performers and supervisors from the rework area. The objective of the Kaizen event was to reduce rework processing time, improve organization, and reduce the workspace. The team took several steps to achieve these goals:
- Helped analyze the process through value stream mapping, identify possible root causes using a fishbone diagram, and brainstorm solutions/improvements.
- Plotted the solutions on a value vs effort graph to target the gems and the low hanging fruit categories.
- Created a detailed rework area current process flow along with cycle time for each step.
- Used the value stream map and cycle times to eliminate all non-value-added steps.
- Measured all dimensions of equipment and used AutoCad to create an accurate current layout of the rework area.
- Brainstormed different layouts of equipment and used spaghetti diagrams to show the most efficient layout.
- Implemented a new layout that reduced the space required to 41% of the previous layout and decreased the cycle time from 60 seconds to 40 seconds per box.
- Assisted the team in presenting the results to higher management.
- Designed a new multi-purpose table using AutoCad Inventor to serve as a tabletop to process rework boxes, a box shelf that can hold up to 135 boxes, and a bag holding rack. The design was handed over to the maintenance team for fabrication.
Floor Waste Reduction on Loin Line
One of my projects involved reducing waste on the loin line. Initially, I focused on a specific conveyor that was identified as causing high levels of floor waste. The first step was to measure the impact of this waste, which involved collecting and weighing waste over two days. The calculated average revealed a significant annual loss of around 16500 CAD.
Upon identifying the problem, I consulted with the maintenance team to brainstorm potential solutions. I also checked the loin line blueprints to understand why the conveyor was causing such high waste levels. It became evident that the conveyor was not designed for the product it was handling.
Eventually, I contacted the equipment supplier to discuss the issue. We decided to install a rotary scrapper for the conveyor. After getting the necessary approvals and purchase orders, the solution was implemented. This resulted in a significant reduction in waste and saved costs.
5S Event for Maintenance Shop at a Feed Mill
I was privileged to introduce the 5S concept to a Feed Mill Maintenance Team. In a comprehensive presentation, I explained the principles of this methodology and how it could be applied to improve the organization of their maintenance shop.
The team was engaged and eager to apply the methodology, and we embarked on the process together. The sorting phase was challenging as it required us to decide on the necessity of each item in the shop, and categorize them accordingly. We used a value versus effort graph to prioritize our actions and manage our efforts effectively.
Documenting the entire process was an important part of our work. We took care to capture the state of the shop before and after the application of 5S principles. The transformation was significant and led to improved efficiency in the shop. We also compiled a report for the mill management and shared the lessons we learned through the process.
Feed Mill Pelleting Improvement
Our Feed Mill was initially designed to produce 4800 Tonnes/week, which is equivalent to 250KT per year. However, the baseline production before the commencement of this project was 4300 Tonnes/week, a performance lag attributed to downtime, specifically due to pellet Mill plugging.
Through dedicated efforts, we managed to increase the production capacity to 5600 Tonnes/week or 290KT per year. This improvement of 30% was a significant achievement. Our efforts also led to a decrease in the average plugs per week, from 12 to just 1.3, reducing overtime hours and saving $680K per year.
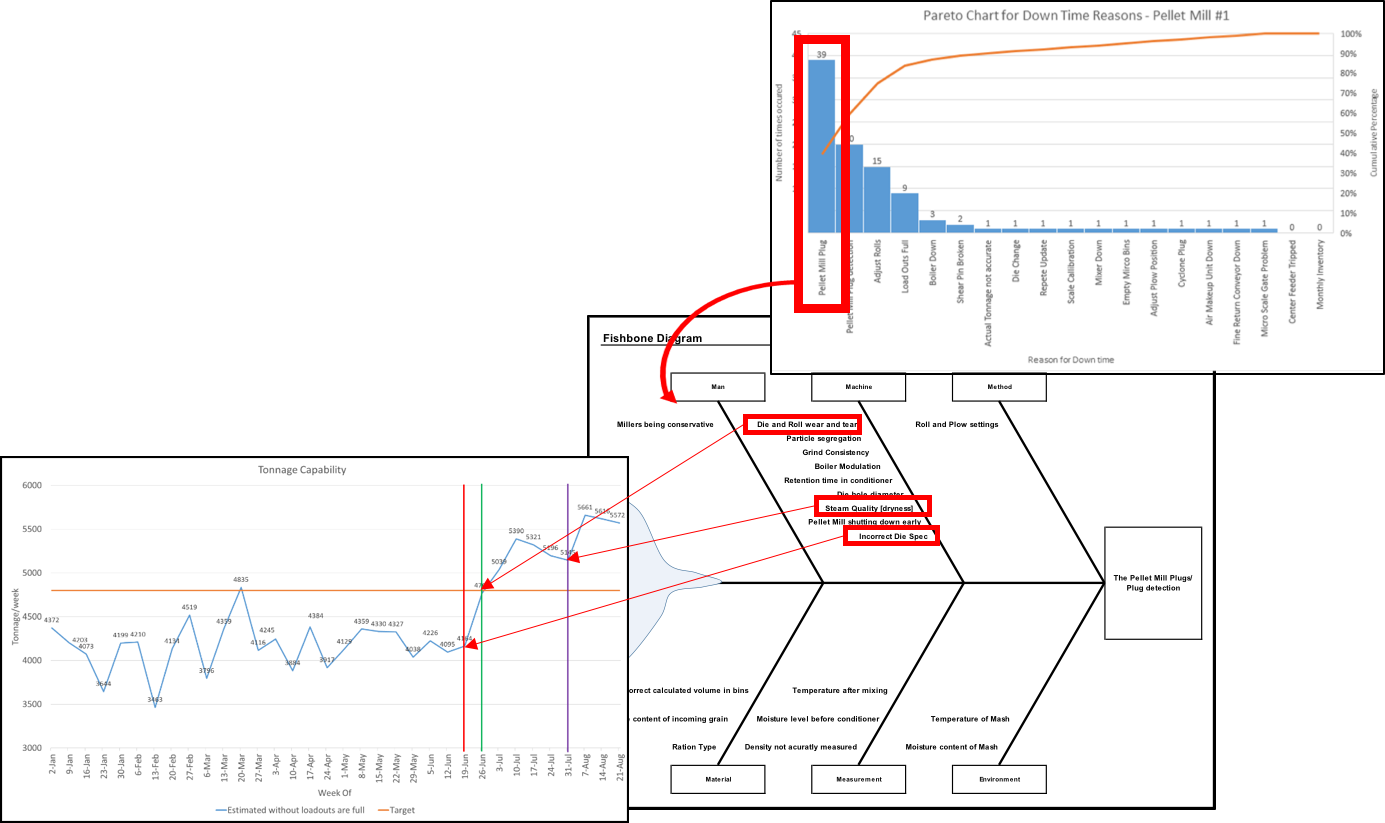
Batching Downtime Improvement
The Randolph Feed Mill is capable of producing feed at a rate of 52 tonnes per hour. The process begins with mixing the ingredients in a process known as batching, before the feed proceeds to the main process, pelleting. By design, the batching process is meant to have an average output of 60 tonnes per hour.
To optimize the process, we performed the 8 steps of process understanding which include identifying process owners and stakeholders, defining process purpose and output, understanding customer needs, measuring process performance and establishing a baseline, and identifying sources of variation. A detailed linear process flowchart was created for every step in the feed-making process, and time studies were conducted.
Note: This section is still under construction.
Hog Stress Effect on Meat Quality
Under Construction.